UN Climate Change News, Bonn, Oct 26 – The global cement industry is taking increasing climate action, encouraged by changes in policy, technology and new opportunities to raise profits and cut costs through reducing greenhouse gas emissions.
The full and willing participation of a sector which accounts for 5-6% of global emissions is critical to contribute to the goal of the 2015 Paris Climate Change Agreement to limit global warming well below 2C degrees and as close as possible to 1.5.
“Ensuring that the cement sector aligns with decarbonization trajectories is critical given the scale of the industry,” said Felix Preston, Senior Research Fellow in the Energy, Environment and Resources Department at Chatham House.
While there is a long way to go before that happens, the experience in other industry sectors has shown that once businesses begin to see that greater action to cut emissions quickly improves both their corporate profile and bottom line, then change speeds up.
Companies like Germany’s HeidelbergCement with its carbon dioxide reduction plans and India’s Dalmia Bharat with its renewable energy programme have taken a lead.
Meanwhile, technology development - from smog-eating building tiles in Mexico to cement that sucks carbon-dioxide (CO2) from the air in Canada - are creating new horizons where cement could become one of the solutions to climate change rather than one of its problems.
Greening the cement sector has the added major benefit of improving public health by removing the gaseous and particulate emissions from cement plants, which harm the environment and can make people sick.
Key Ingredient for Building Infrastructure
In a twist of connected fate, it is also urgent to transform the heavily polluting and energy-hungry industry as soon as possible because countries are going to need a lot more cement in future to build new infrastructure that can better protect societies and economies from the extreme weather that existing climate change is bringing.
Concrete is the second most used substance on Earth after water. Cement is the main component of concrete and is produced globally to build housing, bridges, roads, highways and dams. Demand for cement is largely driven by domestic consumption due to the easy availability of raw materials and high transportation costs.
The cement manufacturing process is resource and energy intensive due to the extreme heat required for production. For example, large amounts of fossil fuels are used to heat a high temperature kiln to around 1400°C and decompose limestone and other raw materials to form a substance called clinker, which is then combined with gypsum to make cement.
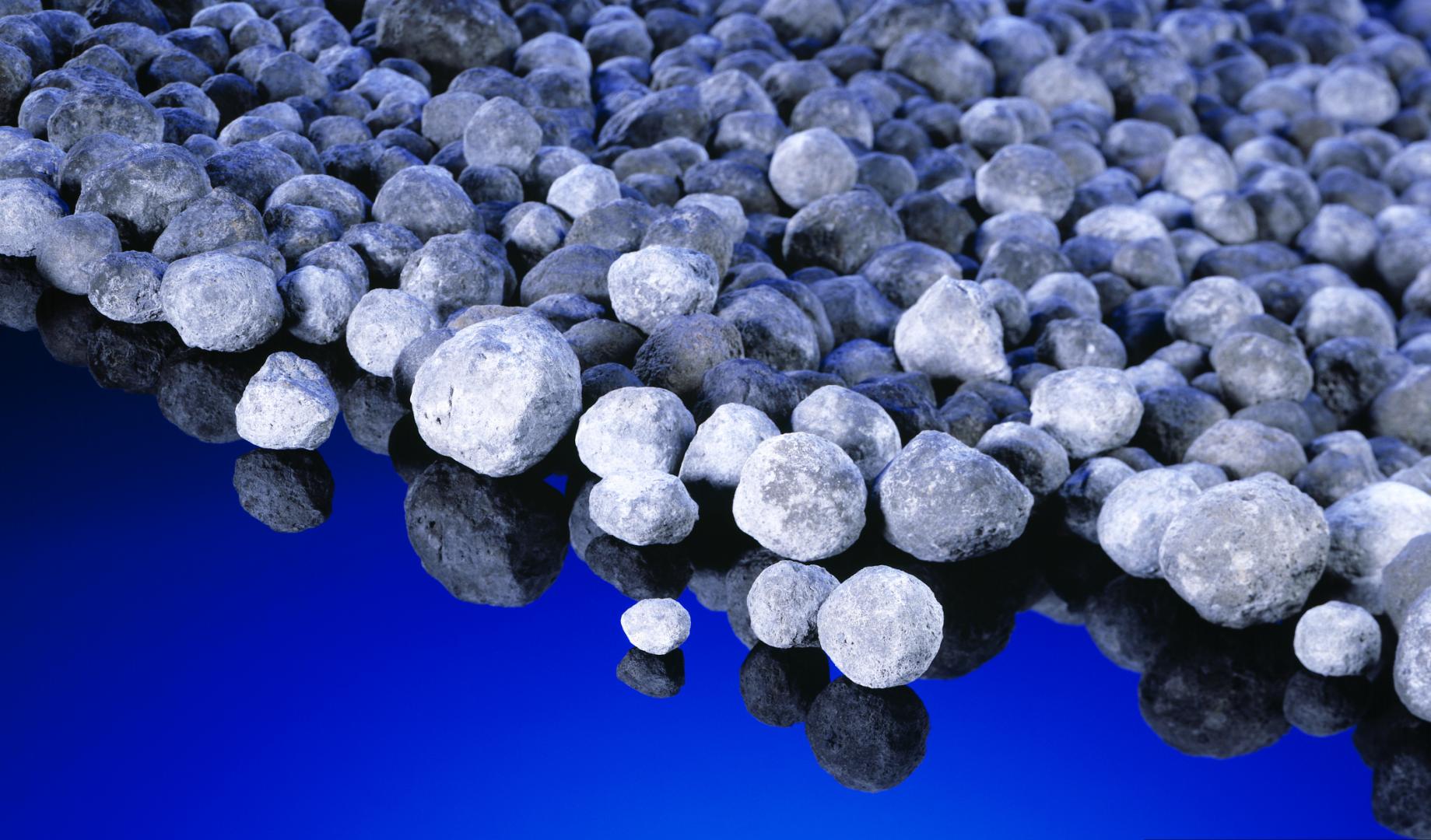
Production of clinker, an intermediate product, results in high carbon emissions. Photo credit: HeidelbergCement
Depending on the variety and process, plants require 60-130 kg of fuel oil and 110 kWh of electricity to produce each tone of cement. For every tonne of cement made, the process releases approximately a tonne of carbon dioxide. Around 50% of emissions come from producing clinker, 40% from burning fuel and 10% from electricity use and transportation.
Clearly, as countries act to implement the ambitious national climate action plans on which the Paris Agreement’s success ultimately rests, they will increasingly need to ensure that bidding for building projects under these plans are awarded to companies that have the lowest carbon footprints as well as the most competitive costs.
Emerging Action – Concrete Results for Climate and Companies
The Cement Sustainability Initiative (CSI) of the World Business Council for Sustainable Development (WBCSD) is a collaboration between 23 major cement producers, operating in over 100 countries and accounting for 30% of world cement production, to pursue sustainable development.
CSI Managing Director Philippe Fonta explained the importance of measuring the level of emissions and preparing a practical action plan.
“The first crucial step to mitigate the impact on climate is to properly monitor the CO2 emissions from cement manufacturers. CSI member companies commit to develop a climate change mitigation strategy and to report their CO2 emissions, reduction targets and progress toward reaching those targets.”
The Cement Action Plan of the Low Carbon Technology Partnerships initiative (LCTPi), also under the WBCSD, aims to accelerate the deployment of low carbon solutions. Two years ago, the industry announced its plan to reduce carbon emissions by 20-25% by 2030, calling for a policy framework and the removal of constraints to achieve the industry’s full reduction potential.
In fact, there are several emissions mitigation options for cement manufacturers including energy efficiency improvement, use of recycled and waste materials, deployment of low carbon fuels and processing of cement at lower temperatures.

Cement plant in Gorazdze, Poland (Photo credit: HeidelbergCement)
“Of the four well known levers – energy efficiency, alternative fuels, clinker substitution and Carbon Capture and Storage – there is untapped potential for clinker substitution in particular which is already resulting in a global saving of approximately 500 million tonnes of CO2 per annum. Smart devices that track and monitor operations or applying machine learning to improve process control at plants could save 10% of fuel used in cement production,” said Chatham House’s Felix Preston.
CSI member companies have made commitments to establish emission reduction targets and to invest further in decarbonization, in support of the Paris Agreement. Philippe Fonta emphasizes that companies can innovate their way through these challenges and reap dividends in the long term.
“Reduction in CO2 emissions often contributes to savings with the overall energy bill. Some incentives can be gained through the future flexible mechanisms that the Paris Agreement will set up, or through financial support to R&D for low-carbon technologies development and deployment. Reducing CO2 emissions is also (often) a condition to maintain the license to operate in the sector,” he said.
Turning Challenges into Opportunities
As well as smog-eating tiles and CO2-sucking cement, another high-tech example is from Italcementi. In sunlight, the active ingredient in this cement captures pollutants in the air and converts them into inert salts, helping to purify the atmosphere from smog.
The mortar is made from 80% recycled aggregates, part of which consist of scraps from the cutting of Carrara marble, which also makes the material whiter. It has already been used to build the Palazzo Italia, in Milan.
But big companies are also taking immediate action to green the traditional cement industry.
Take the case of HeidelbergCement, one of the world’s largest companies for building materials. Implementing an externally verified plan for CO2 reduction, HeidelbergCement is focusing primarily on increasing the use of CO2-neutral fuels and alternative raw materials that are produced as waste in other industries. A large share of such secondary raw material comes from the metalworking industry.
With these measures the company says it has reduced net CO2 emissions by 22 percent to 598 kg CO2/tonne cement, between 1990 and 2016. Through innovative technologies for the storage of CO2 and its use as a raw material, HeidelbergCement plans to lower CO2 emissions even further between now and 2030.
India’s Dalmia Bharat is another leading cement manufacturer undertaking measures to use eco-friendly raw materials and to replace natural resources by utilizing the waste generated from other industries. With a group carbon footprint of 493 kg CO2/tonne of cementitious material, the company boasts of delivering one of the least carbon-intensive cement operation in the world.
In 2015-16, the company said it achieved a 16% reduction in its carbon footprint. The group is focused on increasing the proportion of blended cement in its overall production mix which is considered more environmentally friendly over the usual cement varieties.
Last year, Dalmia Cement also became the first cement company to join RE100 – a global initiative of the world’s leading companies committed to 100% renewable power.
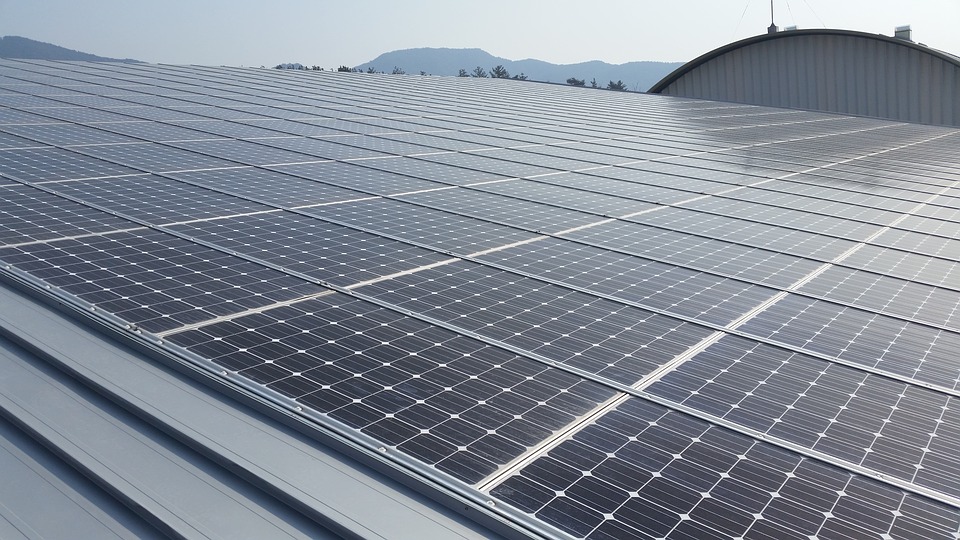
Replacing fossil fuels with renewable energy contributes to reducing carbon emissions (Photo credit: Pixabay)
Large cement companies taking a lead role in accelerating the use of low carbon solutions is a very welcome sign, but any reduction in greenhouse gases might get overshadowed by the expected increase in production without the proper policy checks and balances in place.
So although cement demand from China’s booming economy may soon peak, emerging economies such as India, Brazil and Indonesia are increasingly focused on rapid infrastructure development which, coupled with further urbanization, will likely continue to boost global concrete demand.
Policy and Technology – Key to a Low-Carbon Cement Future
An industry challenge to embrace low carbon measures is that new technologies demand considerable investment in new facilities. Companies need to walk a careful path between producing a high quality, eco-friendly product and achieving profit targets.
In this case, long-term profitability and competitiveness must win against short-term return, supported and assisted by focused and coordinated government policy.
Mr Fonta explained: “Phasing-out outdated kiln technologies by state-of-the-art dry kilns represents huge capital investment costs, with a long return on investment. There is actually limited scope for retrofitting ancient technology.”
Felix Preston from Chatham House noted the challenges involved in disseminating best practices, especially in an industry which is concerned with safety and material performance, but said there are ways to speed up deployment.
“Rapid shifts could be delivered through smart public procurement, and incentives and regulations encouraging the use of waste materials in cements. New industry standards are needed to accelerate the adoption of low carbon cement. Some cities are already seeking to build a market for low carbon cements.”
Mr Fonta said that reducing CO2 emissions goes hand in hand with operational efficiency and can help companies build a competitive advantage through differentiation in their offer of products and services to the construction sector.
But companies that take half-hearted measures to cut emissions or continue to make investments into the production of high carbon cement may face barriers due to CO2 taxes and government regulations or risk their plants becoming stranded assets.
Stranded assets are assets that lose their value due to restructuring of the industry or are abandoned owing to environment related risk factors.
A recent study on stranded assets and renewables from the International Renewable Energy Agency (IRENA) showed that ongoing efforts to reduce greenhouse gas emissions will make a significant impact on the building industry, leaving a large number of buildings as stranded assets.
Technology Development Must Speed Up
Could cement plants with inefficient energy systems suffer the same fate?
Dolf Gielen, Director of IRENA Innovation and Technology Center in Bonn and co-author of the study, points out that around two-thirds of emissions are process emissions in the cement production process so potential for shifting fuel to cut down on emissions has a limit.
“Availability of alternative cementing materials is also limited. So cement will continue to remain in demand, unless tomorrow a new material with cementing properties is discovered and all standards are rewritten overnight. As a consequence, cement plants may not face an immediate stranded assets problem but they will have to confront with serious long term emissions challenges,” Gielen explains.
Mr Preston too underscores the importance of making wise investments and managing exposures to climate risks to prevent asset stranding. “Cement plants and kilns are expected to last around 30-50 years. Low carbon technologies that do not require new kilns or heavy infrastructure investment can be attractive in the short-term. But, investment in low carbon production would help avoid future risks of stranding, especially where new plants are needed.”
And this is an area where financial incentives and government support will be required to fund research, pilot projects and help companies reinvent themselves to meet significant long-term capital expenditures.
A relevant regulatory framework will need to be developed in order to recognize and promote waste co-processing in cement kilns within national waste treatment strategies.
Provision of tax credits for Carbon Capture and Storage and Utilization through emissions trading schemes, in addition to clean energy funds would encourage companies to make the required shift and in the process increase the long term asset value of their plants.
To keep pace with a changing world, innovation and investments into new technologies for low carbon, energy efficient cement plants are needed.
So, while the current climate change challenge for the cement industry may seem to pose a threat to the long-term viability of the sector, it certainly presents a defining moment for the industry to lay the foundation for a low carbon future for everyone.